Hot melt units & autofeed systems
The tank and unloaders primary responsibilities are to melt the adhesive and pump it to the required location through heated hoses. The tanks and unloaders also serve as the temperature sensing and controlling center for the gluing system. Most included a microprocessor control that monitors the temperatures and regulates them accordingly.
Pump options
Piston Pump: The piston pump is used primarily in packaging applications. The piston pump provides high adhesive output as well as high pressures which are ideal in applications where multiple beads and valves are activated at the same time. Piston pumps are required for applications firing bottom up or in horizontal fashion as their high pressure output gives the best possible instantaneous glue output.
Gear Pump: The gear pump is used primarily in applications involving high viscosity adhesives and/or where there is a requirement for very controlled and metered adhesive output. However, they can also be used in low volume packaging applications where small volumes of adhesive are required. Gear pumps deliver adhesive at a very constant and consistent pressure, controllable with a "pressure relief valve" located on the back of each gear pump unit. Gear pumps can also provide line speed tracking without the use of an EPC when they are equipped with a variable speed motor drive which can increase or decrease pressure depending on parent machine speed.
|
|
|
|
|
|
|
|
|
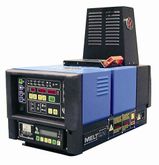 |
|
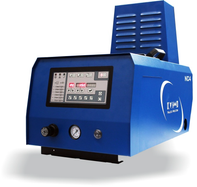 |
|
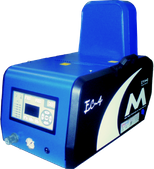 |
|
|
- Micro-processor controls with a wide array of features
- PID control system for accurate & controlled temperature
|
|
- PID control system for accurate & controlled temperature
- Simplify installation with a universal footprint
|
|
- Quick & easy configuration
- Accurate & uniform temperature control
- Uses EVA & PSA compatible with Nordson 2300 & 3000 series
|
|
|
|
|
|
|
|
|
|
|
|
|
|
|
|
|
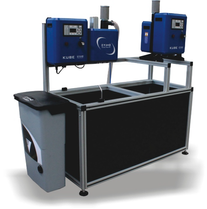 |
|
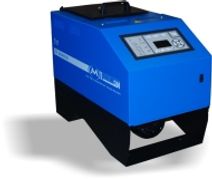 |
|
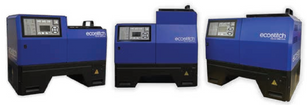 |
|
|
- Promote adhesive stability & reduces char
- No more plugged nozzels. Automatic feeding keeps contaminants out
- Multiple mount configurations make the Kube suitable for new machine installations
- Auto Pressure Sump feature eliminates pressure when machine is open for safer operation
|
|
- Teflon coated tanks reduce char buildup
- D-10 & D-16 can be easily used in fixed speed
- Several relief valve options
- Spur gear pumps are utilised
- Independent control of each heated zone
- Cartridge style heaters allow easy change out in the field
- Complies with major approval codes world wide
|
|
- Most intelligent, versatile, technologically advanced adehsive melters ever created
- Ethernet IP integration, digital pressure control, adhesive usage data available on screen and full OEM integration with all digital based data.
|
|
|
|
|
|
|
|
|
|
|
|
|
|
|
|
|
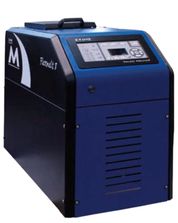 |
|
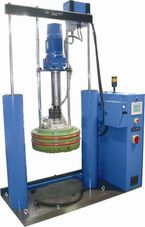 |
|
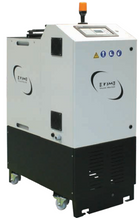 |
|
|
- Utilise up to 2 gear pumps dual or single stream for 8, 14, and 100 liter units
- Manage up to 4 gear pumps dual or single stream with 30 and 50 liter units
- Support any pump combination
- Simplify programming tasks with an easy-to-use, but sophisticated Multi-Function Control with integrated variable speed pump control and intuitive, lanuage-free interface based icons
|
|
- Safer working environment with optional platen protection system and vent hood
- Reduced downtime related to drum changes with new fastening system
- Customisable to specific user needs
- Integrated gammage control
- Teflon encapsulated seals
|
|
- Improved melting grid design makes IsoMelt the units with the highest melting rate in the industry
- Easy removal of adhesive residue allows switching between PUR and other types of adhesive
- Ideally suited for any PUR applications, including those in the automotive, textile, product assembly, woodworking, & PVC industries.
|
|